Hydraulic systems are critical technologies in most industries. It may also be seen in most powering machinery and heavy equipment. A proper hydraulic hose routing system ensures these hydraulic system’s performance and reliability. Without careful attention, the whole hydraulic system may bring various issues. For example, inefficiency, downtime, and safety risks are noteworthy.
This article will highlight the ten best practices for hydraulic hose routing. In addition, we will explore each of these practices more. We will also learn the consequences of ignoring these steps. Therefore, this guide will benefit your actual project. In addition, if you need further help, feel free to contact our professionals.
Hydraulic Hose Routing – 10 Best Practices
When it comes to hydraulic systems, ensuring the proper hydraulic hose routing and installation is crucial. You can ultimately get their effective performance, longevity, and safety by providing this. Following the ten best practices below, you can ensure an appropriate hydraulic hose routing system. We recommend you understand every step and get the best product for your hydraulic system.
Determining The Required Hydraulic Hose Pipe Sizes
The first step that you should do is to identify the required hydraulic hose pipe sizes for your project. For every component, you must know the appropriate measures. You can read the hydraulic hose size chart and relate the dimensions to your hydraulic system. A typical hydraulic hose comes with various specifications. The chart highlights the hydraulic hose manufacturer, standards, and diameter. In some hydraulic hose size charts, you may find working pressure, production dates, and other information.
You should also find the appropriate supporting equipment based on these hydraulic hose pipe sizes. For example, hydraulic hose fittings, support clamps, and protection guards are noteworthy. For hydraulic hose fittings, you can check the hydraulic fittings size chart.
Avoid Twisting Hose Assemblies
The twisting hose assemblies are a common mistake that can compromise a system’s performance. Twisting hose assemblies may come from an inappropriate installation. In addition, some applications may involve torsional stress or excessive rotation force. In these situations, twisting hose assemblies may occur. Twisting hose assemblies creates specific problems like reduced flow and increased wear.
To avoid twisting hose problems, you should carefully plan the routing of hoses. You can consider the shortest, straightest path with minimal bends and twists. You can also use supporting equipment and clamps to secure them in place. However, you can also seek assistance from our customer service. Our team of professionals is waiting for you to respond to your queries.
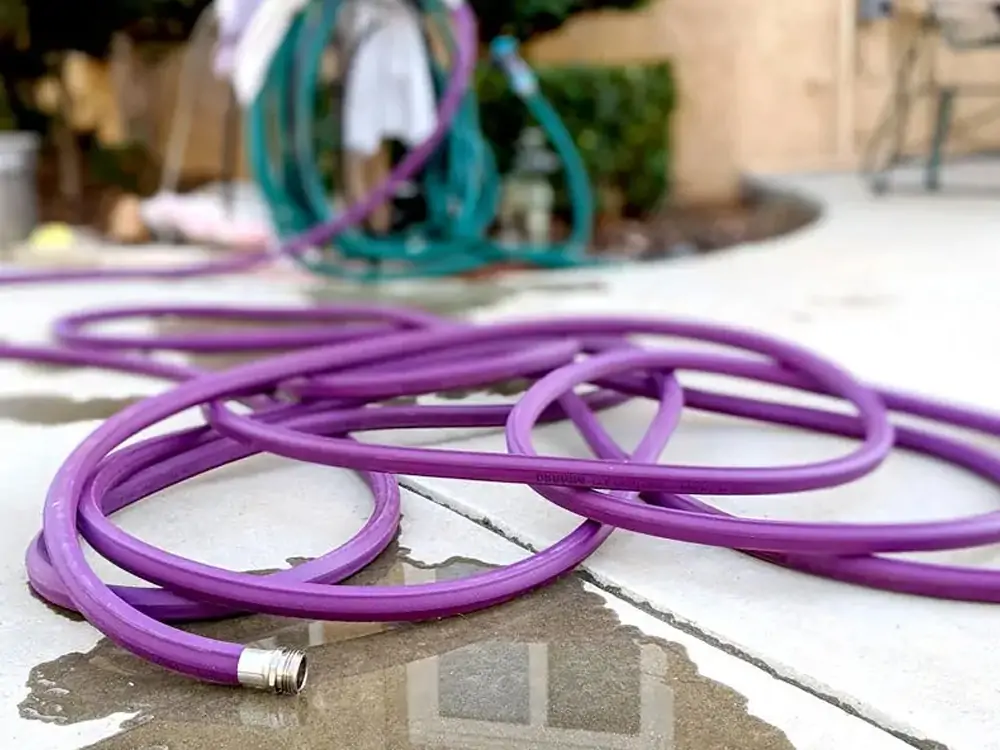
Avoiding Bending The Hose Tightly
Tightly bending hoses is another mistake that can compromise the hydraulic system’s performance. Note that hydraulic hoses are designed to transmit fluid under high pressure. It helps to accommodate the necessary movement. Excessive bending and tight radius bends may affect the hydraulic hoses and the overall system. Therefore, avoiding tightly bending the hose is essential to ensure the proper hydraulic hose routing.
Every hydraulic hose has a specified minimum bend radius recommended by the manufacturer. Always follow their instruction to avoid kinking and damage. The minimum bend radius is the lowest radius to which a hydraulic hose can operate smoothly. Moreover, carefully plan the hose routing before installation. In this case, try to avoid sharp bends and tight corners.
Using Hose Elbows or Hose Adapters
Using Hose Elbows or Hose Adapters can be a helpful technique in hydraulic hose routing. They allow for changes in direction and connection without twisting the hydraulic lines. Hose elbows are also famous as hose bends. They come in various angles, like 45, 60 or 90 degrees. You can also get customized hose elbows depending on your application. On the other hand, hose adapters connect different types of hoses with fittings or other equipment. Hose adapters also come in various configurations and sizes with multiple purposes.
While routing around obstacles or corners, hose elbows, and adapters play a crucial role. Select the right type that matches the specifications and size of the hoses and fittings being used. You can also follow the manufacturer’s guidelines for more information.
Using Appropriate Hydraulic Hose Fittings
We strongly recommend not mixing the hydraulic fittings and hose during installation. In the first step, you have already checked the sizes of hydraulic hoses and fittings. Therefore, stick to your plan during installation and use the appropriate size for the hose installation. Note that the hose fittings you choose must match your hydraulic hose diameter.
We recommend you choose the hydraulic hose fittings from the same manufacturer. Choosing the same brand ensures a reliable hydraulic hose installation. It also provides a safe and qualified hydraulic system. However, consult our expert to learn more about hydraulic hose standards and sizes. You can show them your design layout and get the best recommended options for your project.
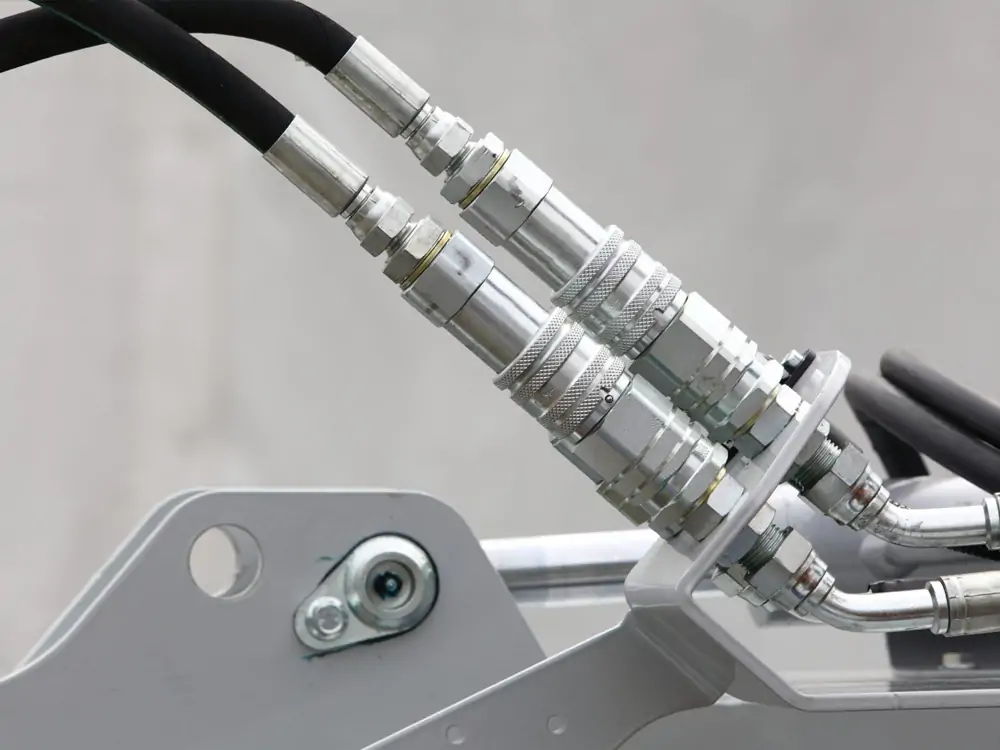
Using Hydraulic Hose Clamps
Hose clamps secure and fasten hydraulic hoses onto their system’s fittings, pipes, or other components. Hydraulic line clamps prevent hose movement, leaks, and damage. By preventing these obstacles, they maintain the safety and efficiency of hydraulic systems. Therefore, a hydraulic pipe clamp is an essential component in hydraulic routing.
Choose the correct hydraulic hose clamps suitable for the size, material, and application. Clamps also come in various types. For example, worm gear clamps, T-bolt, and spring clamps are noteworthy. The choice depends on the type of your hydraulic system and place of application. Moreover, you can place hose clamps at a distance from hose ends and fittings. Note that it ensures a secure grip. Follow the manufacturer’s guidelines or contact our customer support team for more information.
Using Hydraulic Hose Support Clamps
The difference between hose clamps and hose support clamps is simple. They two serve different purposes in hydraulic and fluid transfer systems. Hose clamps usually secure and fasten hydraulic hoses onto fittings, pipes, or other components. On the other hand, hydraulic hose support clamps are designed to support and organize the hoses, cables, or lines. These support clamps do not secure hoses to fittings.
A hydraulic hose holder clamp is also crucial for organizing and securing hydraulic hose routing. They attach hoses to the surface and prevent sagging and tangling. As a result, it can maintain an orderly arrangement. Therefore, selecting the correct type of hydraulic hose support clamps is necessary.
Avoiding Fully Extended Hose Assembly
When a hydraulic system is in running operations, the pressurized fluid slightly decreases the hose length. Consequently, it expands the hose diameter. So, allowing a hydraulic hose assembly in the fully extended state may create undesirable consequences. This repetitive stress may forcefully pull the hydraulic hose from the fittings under pressure. It also significantly reduces the hose’s service life. Ultimately, it may create potential catastrophic failures. Therefore, preventing hose assemblies from becoming fully extended is crucial for maintaining longevity.
To safeguard against this issue, you can incorporate a slight bend or slack into the hose routing design. Note that excess bending may also create problems. Therefore, for a proper bending radius, you can consult a professional to help in your design.
Using Hydraulic Hose Protection Equipment
One of the best practices for proper hydraulic hose routing is using a hydraulic hose protector. A hydraulic hose spiral wrap provides a wide range of benefits. Firstly, it saves hydraulic hoses from abrasion, impact, heat, and chemicals. Secondly, it enhances the hydraulic hoses’s longevity. It also ensures safety by preventing leaks, bursts, and unexpected failures. Overall, it plays a crucial role in maintaining the overall efficiency of a hydraulic system.
If you want to learn more about hydraulic hose spiral guards, you can read our blog post. “Hydraulic Hose Spiral Wrap – Ultimate Guide” explains all the fundamentals. Therefore, selecting a suitable hydraulic hose protector is essential for better routing.
Cleaning Hydraulic Hose Routing
Finally, the last most important practice that you should do is clean hydraulic hose routing regularly. Here, cleaning means reducing the unnecessary length of hydraulic hoses. You can save some space for regular maintenance using hose elbows and adapters. The use of this equipment helps clean up the routing. Ultimately, it extends the hydraulic hose’s life. It also provides easy access to regular maintenance.
Indeed, regular maintenance improves the overall performance of a hydraulic system. It helps prevent blockage, contamination, and damage that can result in costly repairs. During maintenance, don’t forget to depressure and shut down the hydraulic system. Then, blow compressed air through the routing to remove loose contaminants. After that, flush with compatible hydraulic fluid to remove internal impurities. Inspect and check if there is any leak or damage. Finally, reassemble and test the overall system.
Final Thought
Throughout this article, we have discussed the best practices for hydraulic hose routing. Each step is critical to ensuring a hydraulic system’s performance, efficiency, and reliability. By understanding these best practices, industries can safeguard their investments.
This guideline is a summary of the whole hydraulic hose routing procedure. We recommend you consult a professional to get an official hydraulic hose routing system design. You can also reach out to our customer service team. Our dedicated professionals and experienced hydraulic engineers are ready to assist you.